Trade Counter Open Monday to Friday, 8.30am-5pm
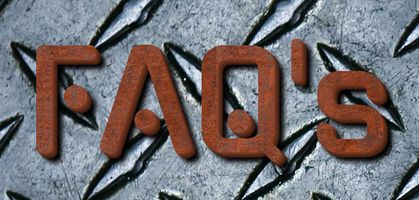
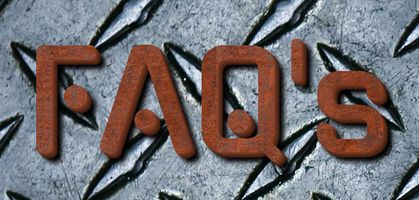
Xtreme Plasma FAQ's
Welcome to the Xtremeplasma.com FAQ page! Here you'll find answers to the most common questions about plasma cutting, CNC plasma systems, MIG welding, and TIG welding. If you don’t find the answer to your question here, feel free to contact our support team for more assistance.
CNC Plasma FAQs
1. What is CNC Plasma Cutting?
2. How Does a CNC Plasma Cutter Work?
3. What Are the Benefits of CNC Plasma Cutting?
4. What Materials Can Be Cut with a CNC Plasma Cutter?
5. How Do I Choose the Right CNC Plasma Cutter?
Plasma Cutting FAQs
1. What is Plasma Cutting?
2. How Does a Plasma Cutter Work?
3. What Metals Can Be Cut with a Plasma Cutter?
4. What Are the Advantages of Plasma Cutting?
5. What Thickness of Metal Can a Plasma Cutter Cut?
TIG Welding FAQs
Q1: What is TIG welding?
Q2: How does TIG welding work?
Q3: What are the benefits of TIG welding?
Q4: What materials can be welded with TIG welding?
Q5: Is TIG welding harder than MIG welding?
MIG Welding FAQs
Q1: What is MIG welding?
Q2: How does MIG welding work?
Q3: What are the advantages of MIG welding?
Q4: What materials can be welded with MIG welding?
Q5: What is the difference between MIG welding and TIG welding?
Additional FAQs
Q1: Do you offer tutorials or training on using your equipment?
Q2: How can I get in touch with customer support?
Q3: Do you offer warranties on your products?
Q4: What are the shipping options and costs?
Q5: Do you offer financing options?