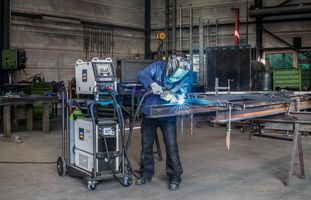
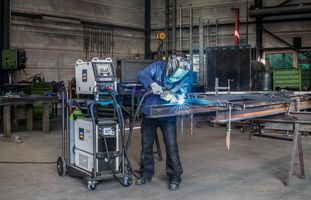
MIG Welders – High-Quality Welding Equipment
Top Brands We Offer
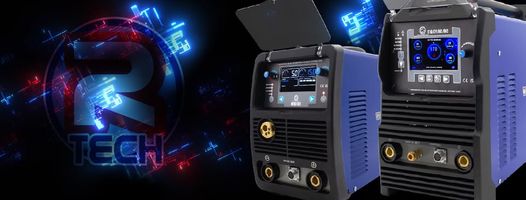
R-Tech Welding
R-Tech Welding has released new MIG 181 and TIG Easyset machines, now available at Xtreme Plasma's Trade Counter, offering enhanced features for various welding needs. These new models aim to provide improved performance and reliability for both professional and hobbyist welders.
GYS in Action
GYS MIG welders offer a range of options, from easy-to-use machines for hobbyists to powerful, advanced models for industrial use. They are known for their quality construction, innovative features like synergic control, and suitability for various applications from automotive repair to heavy fabrication.
All You Need to Know About MIG Welders